Работа над ошибками. "Человеческий фактор" в условиях склада
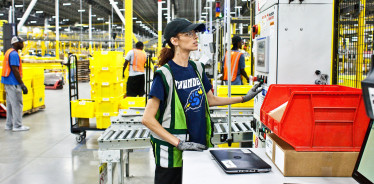
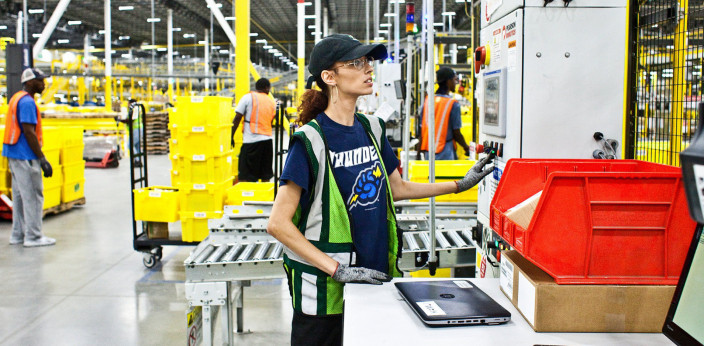
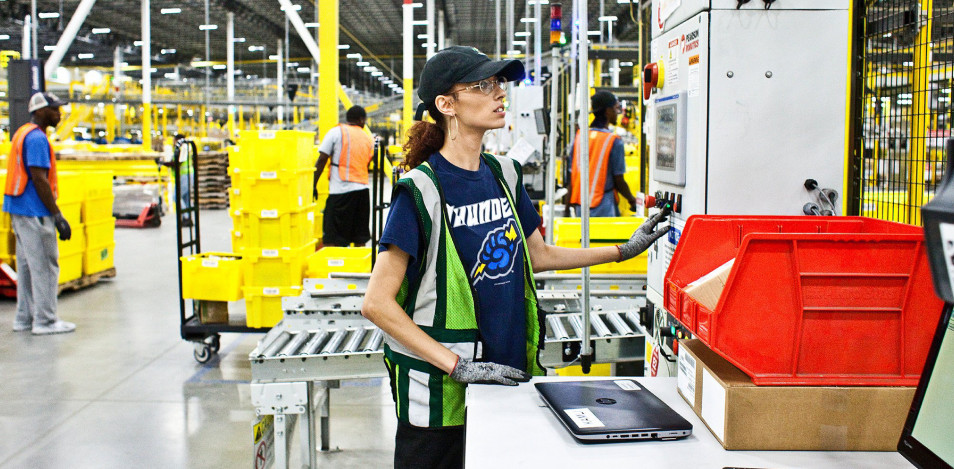
Почему возникают ошибки?
В любом бизнесе человеческий фактор имеет весомое значение, им нельзя пренебрегать. Персонал на складе нередко допускает ошибки, что может повлечь за собой серьезные убытки. И причины могут быть разные: нарушение инструкций и технологии в процессе оптимизации, недостаточный уровень автоматизации и пр.
Робототехника в какой-то мере может быть и надежнее человека, но отсутствие абстрактного мышления, объективное восприятия окружающей среды и множество других факторов, которые свойственны человеку, для машины является недостатком. Например, на складе сотрудник может визуально распознать поврежденный товар или неупорядоченный груз, что неподвластно роботу. Робот-кладовщик идеален при выполнении однотипных задач, он безошибочно способен выполнять четко выстроенные операции. Но при этом стоимость их в разы превышает стоимость ручной работы персонала.
В каждом бизнесе существуют процессы, при которых используя ручной труд нельзя исключить ошибки и тут не обойтись без автоматизации.
Чтобы снизить количество ошибок на складе, как правило, прибегают к использованию терминалов сбора данных, но это работает при условии оцифрованной информации и, если все производственные процессы налажены. Эффективность работы зависит насколько подготовлен персонал, выверенные данные и т.д. В первую очередь необходимо менеджерам правильно организовать рабочий процесс.
К появлению ошибок в управлении приводит нарушение международного стандарта менеджмента качества ISO 9001:2015, основные из них, например:
- при принятии решения игнорируют факты, но полагаются на чьи-то мнения;
- не проанализировав причины, пробовать исправить ситуацию;
- нехватка ресурсов;
- отсутствие необходимой квалификации (навыки, подготовка, опыт) у сотрудников, которым поручают работу.
Нужно учесть и то, что менеджер работает в условиях многозадачности и ограниченных ресурсов, а значит вероятность ошибок не исключена. Чтобы минимизировать ошибки, необходимо придерживаться международного стандарта. К ошибкам со стороны менеджера может привести нечетко поставленная задача, отсутствие понимания, что необходимо сделать исполнителю, а это сказывается на результативности работы.
Оптимизируем процессы
Значительно снизить количество ошибок в работе можно путем непрерывного улучшения всех процессов. Например, в Tablogix применяют "action timing plan" или план действий — отрабатываются предложения сотрудников, используют метод Парето и инструменты lean-менеджмента. Такими действиями объединяется коллектив, оптимизируется работа в структурных подразделениях.
Среди основных подходов борьбы с ошибками можно выделить:
Zero Tolerance (Gemba) — научиться принимать решения на месте по ситуации. На складе нужно контролировать точность и ход работы. Так, если в какой-то зоне беспорядок, то это непременно приведет к низкой производительности, например, при комплектации заказа. Данным методом предлагается фиксировать ошибки, и потом проводить мероприятия по исправлению и отслеживанию ситуации в дальнейшем после исправления.
Система 5S (Lean Management) – это алгоритм для устранения замечаний и организации рабочего пространства. Такой подход предусматривает создание наилучших условий для выполнения операций, соблюдения порядка, чистоты и оптимизации складских процессов на пяти правилах:
- Сортируй;
- Создавай;
- Содержи в чистоте;
- Стандартизируй;
- Сохрани достигнутое.
План действий (Action and Timing Plan) – инструмент контроля, предусматривающий план действия с последовательными этапами достижения цели.
Предложения по улучшению (Employee Improvement Suggestions) — этот подход дает возможность сотруднику предложить варианты, например, оптимизации в структурированной форме. В случае достижения цели, он может быть поощрен за счет бонусной системы.
Лист непрерывных улучшений (Continuous Improvement Worksheet) представляет собой упрощенную форму вышеизложенного предложения (Employee Improvement Suggestions), такой лист крепится к стенду. Сотрудники вписывают в соответствующие поля предложения как снизить риск ошибки и оптимально построить рабочий процесс.
Кружок качества (Quality Team Circles) – это своего рода стратегическая сессия для сотрудников всех уровней. На таких сборах коллектива проводят дискуссии и совещания по итогам прошедшей недели, например, что можно улучшить и на что обратить особое внимание. Делают заметки изложенных замечаний, и формируют план действий по их улучшению.
Шесть сигм (Six Sigma) – метод оптимизации процессов за счет статистической оценки фактов и данных, используется набор разных инструментов качества. Разработана эта концепция компанией Motorola еще в 80-е годы.
Метод четырех диаграмм (QOS Methodology) включает следующие шаги:
- Определите цель и отслеживайте тренд с помощью диаграммы, сверяйте эффективность показателей.
- Сделайте анализ проблем по методу Парето. Диаграмма покажет, какие наибольшие ошибки создают неблагоприятную тенденцию.
- Постройте план действий корректировки ошибок.
- Контроль за выполнением.
Анализ (Failure Mode and Effects Analysis, FMEA) - выявление наиболее критических сегментов в процессах методом анализа видов и последствий отказов с целью управления качеством.
Метод 8D основывается на поиске первопричины ошибки и разработки решения, дабы не повторить ее. Такой метод является первым шагом к повышению качества и надежности продукта, который не удовлетворяет клиента.
Отчет необходим для предотвращения повторных ошибок. Исследования, анализ и предпринятые корректирующие действия будут использоваться, как ответ в решении проблемы.
Бенчмаркинг (Benchmarking) или эталонное тестирование – такой метод необходим, чтобы минимизировать ошибки на примерах других компаний. Понимая ошибки других, не придется учиться на своих. Данный анализ поможет улучшить собственную работу, что повысит эффективность функционирования бизнеса в целом.
Коммуникация – это основной способ предотвращения ошибок.
Мотивируйте сотрудников улучшать свою работу, прибегая к наглядным примерам. Например, показатели эффективности и производительности можно разместить на стенде. Статус того или иного показателя будет мотивировать персонал повысить их или сконцентрироваться на работе без ошибок, чтобы не подводить остальных и т.д.
Это далеко не все аспекты работы над ошибками, некоторым компаниям, чтобы повысить эффективность работы склада, например, достаточно заменить WMS-систему, если изначально рассматривались решения на платформе 1С. В любом случае, главное понимать свои потребности и это будет залогом успеха.