Наші
проєкти
Склад Сервіс вже реалізував більше 25 000 проєктів з використанням різної продукції. Ми реалізовуємо найрізноманітніші та цікаві задачі, включаючи новаторські рішення зі всього світу.
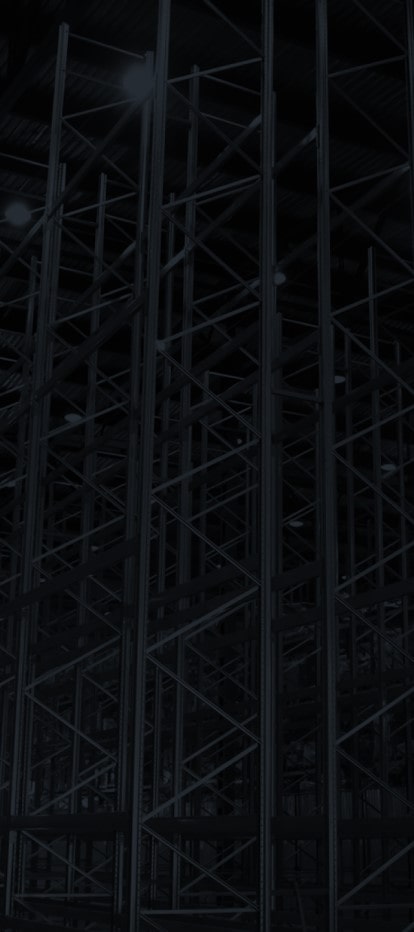
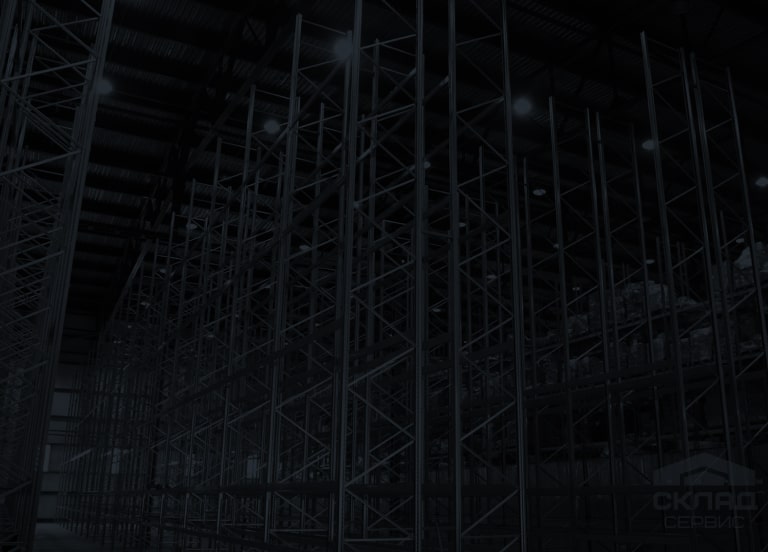
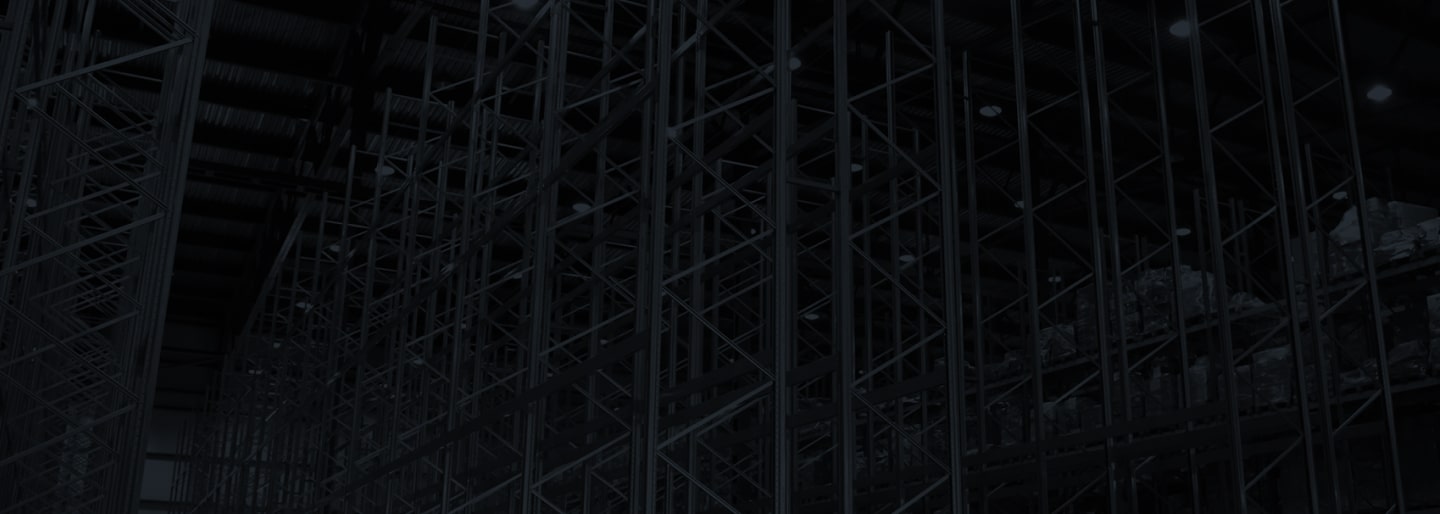
Знайдіть проєкт, що вас цікавить
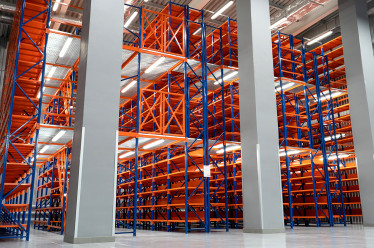
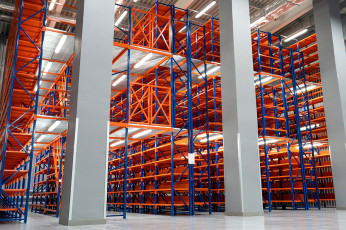
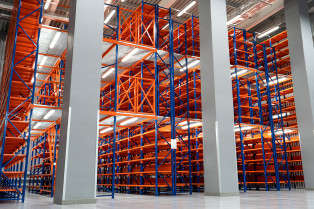
22.07.2025
Ключові особливості рішення:
Триповерховий мезонін: Забезпечив ідеальні умови для зручного та швидкого сортування дрібного товару завдяки повноцінним, фіксованим коміркам зі спеціальними перегородками.
Палетні стелажі: Оптимізували зберігання великогабаритних та палетованих вантажів, забезпечуючи легкий доступ та високу вантажопідйомність.
Усі елементи системи покриті спеціальним порошково-полімерним покриттям, що гарантує виняткову гігієнічність, стійкість до корозії та легкість у догляді критично важливі фактори для фармацевтичної продукції.
Стелажі обладнані фронтальними відбійниками, захистами торців ряду та обмежувачами палет. Додатково, у зоні приймання товару встановлено інноваційні самозакриваючі ворота, що відкриваються за допомогою навантажувача, значно підвищуючи безпеку та ефективність логістичних операцій.
Технічні характеристики:
Мезонін: розмір полиць 1000х600 мм; навантаження на полицю 75 кг; висота перекриття: 2400 мм; загальна виcота мезоніну: 7000 мм.
Палетні стелажі: розмір секції 2700х1100 мм, навантаження на рівень зберігання 1500 кг та 3000 кг; висота палети: 1200 мм; висота рами: 6200 мм.
Результати впровадження
Цей проєкт став яскравим прикладом того, як індивідуальний підхід та глибоке розуміння потреб клієнта дозволяють створювати не просто стелажні системи, а повноцінні логістичні рішення. Ми успішно розробили та реалізували систему, яка не тільки оптимізувала складські процеси та простір, але й повністю відповідає найвищим стандартам фармацевтичної логістики та безпеки зберігання медикаментів.
Завдяки впровадженню нашого рішення, логістична компанія отримала:
Збільшення ефективності зберігання на 200% порівняно з попереднім рішенням.
Підвищення швидкості обробки вантажів на 35% завдяки оптимізованим маршрутам.
Повну впевненість у безпеці та цілісності продукції з показником збереженості 99,2%.
Економію експлуатаційних витрат на 15% щорічно за рахунок зниження трудозатрат.
Час реалізації проєкту: 8 робочих тижнів.
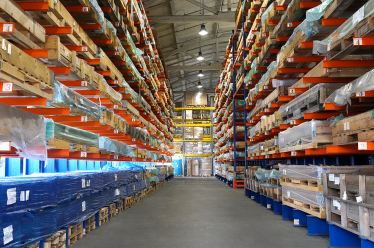
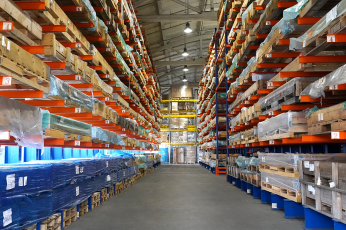
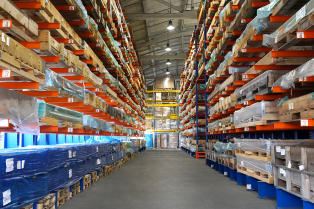
07.05.2025
Для вирішення проблеми ми запропонували впровадження консольних стелажів, спеціально адаптованих для зберігання довгомірних і великогабаритних вантажів, таких як мармурові плити. Ці стелажі дозволили оптимізувати простір і значно покращити операційну ефективність складу.
Що отримав Агромат завдяки консольним стелажам?
Скорочення площі зберігання втричі: Завдяки продуманій конструкції стелажів складський простір став використовуватися значно ефективніше, звільнивши місце для інших потреб.
Подвоєння висоти зберігання: Стелажі висотою 8710 мм дозволили зберігати плити вертикально, що вдвічі збільшило місткість складу.
Організація окремих комірок для мармуру: Кожна позиція отримала власну комірку, що спростило доступ до потрібної плити без необхідності переміщення інших.
Оптимізація операційних проходів: Ширина проходів (3600 мм) і воріт (4600 мм) забезпечує зручність роботи з плитами, прискорюючи їх обробку.
Швидкий доступ для клієнтів: Плити тепер легко знімаються зі стелажів для демонстрації, що усуває затримки та робить вибір зручним і швидким.
Технічні характеристики:
420 палетомісць для зберігання плит із мармуру
Навантаження на руку — 400 кг(до 1200 кг на палетомісце).
Довжина консольного ряду — 40800 мм.
Завдяки консольним стелажам Агромат не лише оптимізував складське зберігання, але й підвищив якість обслуговування клієнтів. Процеси стали швидшими, а склад запрацював як злагоджений механізм, що забезпечує ефективність і конкурентну перевагу.
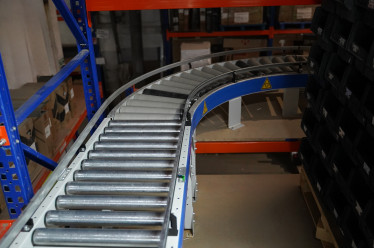
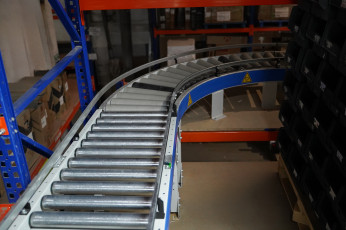
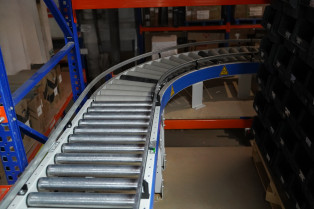
11.02.2025
Переглядаючи аналогічні кейси від нашої компанії, замовник звернувся до Склад Сервіс. Нами було запропоновано кілька варіантів, які можна масштабувати та інтегрувати з існуючим мезоніном. І саме конвеєрна гірка стала тим ключем для вирішення проблеми. Наші інженери розробили фінальне креслення для оптимального розташування, враховуючи потреби клієнта та економію простору.
Конвеєрна гірка — масштабоване рішення, яке інтегрується у простір складу без складного монтажу. Чому саме гірка?
Мобільність та гнучкість.
Гірка може бути масштабована до 5-ти рівнів. Модульна конструкція легко демонтується і може бути перевезена та встановлена на новій локації.
Автоматизація та економічність.
Завдяки інтегрованим датчикам робота гірки активується автоматично, та автоматично зупиняється коли транспортування товару не потрібно. Датчики запускають систему лише при наявності вантажу.
При цьому має низьке енергоспоживання: всього 1,5 кВт, що еквівалентно до роботи одного електрочайника.
Конвеєрна гірка — приклад того як прості рішення можуть зробити вашу логістику ефективнішою. А ми допоможемо адаптуватися до нових викликів, модернізуючи ваш склад з урахуванням усіх потреб та можливостей.
Мобільне, та енергоекономічне рішення яке приносить результат вже зараз. Оптимізуйте свої процеси разом зі Склад Сервіс!
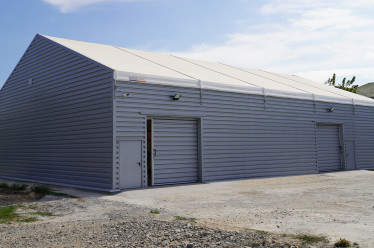
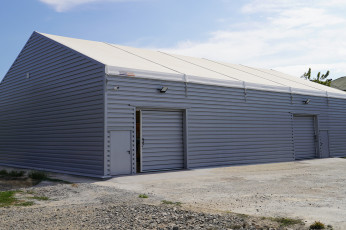
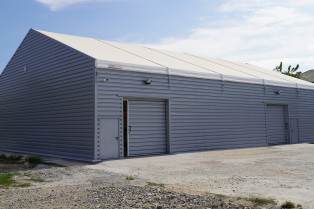
04.02.2025
Увага до матеріалів та ощадливість – один з факторів успіху компанії.
Склад з алюмінієвих конструкцій має модульну структуру, що дозволяє легко змінювати його розміри: розширювати або зменшувати, залежно від потреб клієнта. Споруду можна легко демонтувати та перенести на інше місце, що забезпечує адаптивність до змін бізнес-стратегії.
Стандарти у всьому: від авто до складу. Стандарти, відповідні високому рівню сервісу компанії з понад 100-літньою історією творення технологій.
Технологія будівництва швидкомонтованих споруд поєднує ергономічність, мобільність і технологічність, що ідеально відповідає сучасним вимогам.
Ця конструкція забезпечує: • Швидкий монтаж без капітального фундаменту – можливість встановлення на ґрунт, плита, щебінь, бетон, асфальт тощо. • Відсутність потреби в дозвільній документації, оскільки це збірна модульна споруда. • Мінімальні логістичні та монтажні витрати у порівнянні з традиційним будівництвом. • Модульність і мобільність: можливість розширення, зменшення або переміщення складу. • Енергоефективність: світлий простір, що дозволяє працювати без штучного освітлення у денний час.
Готові до вашого виклику! Втілюйте високі стандарти разом зі Склад Сервіс.
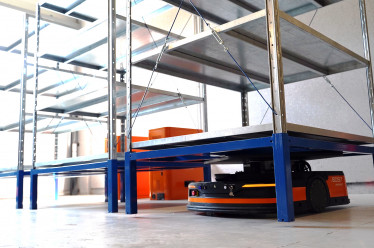
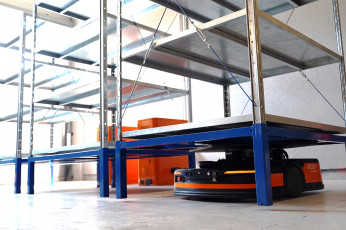
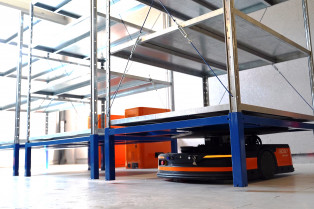
16.12.2024
Український Амазон? Так, це реально!
Компанія Viatec, яка вже 16 років розробляє передові рішення у сфері безпеки, зробила сміливий крок у майбутнє. Ми стали частиною їхнього інноваційного складу, розробивши спеціальну стелажну систему, яка ідеально підходить для роботи з AGV-роботами, які самі планують маршрут та перевозять до 600 кг вантажу.
AGV– це автоматично керовані транспортні засоби, який зазвичай називають просто «роботами». Принцип їх дії доволі простий:
Від працівника робот отримує задачу щодо переміщення вантажів в межах складу. Це відбувається через автоматизовану систему, яка у реальному часі відображає кількість одиниць техніки та місце їх перебування. Оператор, що спостерігає за операціями, задає техніці точку доставки вантажу. Система знаходить вільний юніт, який знаходиться ближче до точки приймання вантажу. Опісля система передає роботу вхідні та вихідні дані, а саме QR-коди. Саме за ними робот розуміє, куди рухатися.
Як це відбувається?
Роботи переміщуються за позначеними лініями, що на шляху містять QR-коди. Аби зрозуміти який стелаж треба забрати робот зчитує QR код, що нанесено на дні стелажа і є унікальним для кожної одиниці. Потім він заїжджає під стелаж та підіймає його. Маршрут до місця призначення прокладає самостійно. Завдяки датчикам робот оминає перешкоди на своєму шляху, а завдяки нашим стелажним Смарт-системам переміщує до 600 кг вантажу.
Розмір конструкції: 1.0 м × 1.20 м
4 рівні з міжполичковим простором 50 см.
Цей полегшений поличковий стелаж займає лише 4,8 м² корисної площі зберігання.
І на останок: реалізація проєкту становила 45 календарних днів з моменту затвердження рішення до моменту передачі клієнту.
Зручно, мобільно, сучасно, швидко. Саме те, що вирізняє смарт склад третього тисячоліття.
Крокуємо разом?
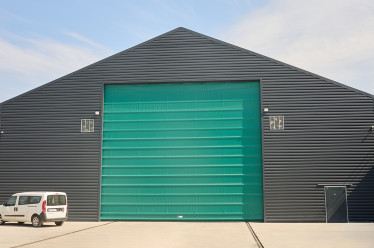
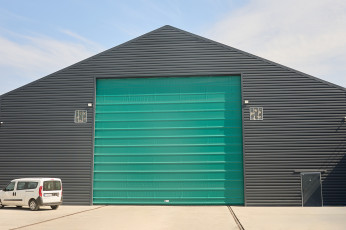
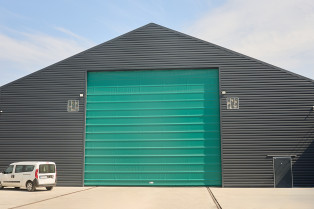
05.11.2024
Цей проєкт вирішує одразу кілька важливих завдань: конструкція дозволяє козловому крану вільно працювати, зберігає логістичні маршрути між цехами і забезпечує виїзд для великогабаритного вантажу. Завдяки спеціальному накриттю, ефективній вентиляції, продуманому освітленню і можливості майбутньої релокації, склад став надійним рішенням для безперервної роботи замовника на час підготовки капітальної споруди.
Виробнича компанія VODALAND працює у сфері збору, очищення, відведення води, інженерного облаштування та благоустрою території. Саме це виробництво займається виробами з склопластику: резервуари, очисні споруди, насосні станції та багато іншого. Поточна виробнича площа компанії містить рейки, якими пересувається козловий кран.
Що таке козловий кран?
Це механізм, що переміщує габаритні вантажі до 8 тонн у горизонтальному та вертикальному положеннях. Конструкція універсальна, але велика. Як і запит від компанії: складний та системний. Все, як ми любимо.
Команда Склад Сервіс має багаторічний досвід та успішно реалізовані проєкти. Кожен наш проєкт має неабиякі особливості. Цей не виключення.
Важливою умовою було накриття поточної площі з наявним краном всередині, що й зробило цей склад найвищим з усіх, що ми реалізовували. Достатня висота споруди складу забезпечує простір для переміщення механізму. Окрім того, ми мали зберегти наявні логістичні маршрути між цехами, організувати можливість виїзду великогабаритного грузу та в майбутньому виїзд портального козлового крана зі складу. Плюс до цього, із зачиненими воротами склад мав забезпечувати комфортні умови роботи, а також ефективну вентиляційну систему.
Зроблено! Проєкт успішно реалізовано, без перебільшення, завдяки професіоналізму нашої команди. Адже робота передбачала складну координацію численних підрядників. Ми одразу чітко розподілили зони відповідальності серед наших партнерів. Склали детальний графік виконання робіт. Зазначили кількість людей необхідних для кожного етапу. Терміни початку і завершення кожного завдання. На практиці це мало вигляд буквально щохвилинного графіка виконання кожного виду робіт. Завдяки цьому ми створили ланцюг виконання, коли одне завдання узгоджено переходило в інше.
Це було дуже важливо, оскільки окрім власної монтажної бригади, завдяки якій монтаж споруди тривав лише 5 тижнів, в проєкті брали участь декілька підрядників. А саме: підрядники з гідроізоляції, нівелювання, вентиляційних робіт, підрядник з виготовлення промислових воріт а також освітлення та електромережі.
Що було викликом для нас?
1. Пошук і розробка рішення стосовно воріт для виїзду крана.
Ми проаналізували безліч варіантів та спроектували декілька своїх для організації великого проїзду зі складу з можливістю закриття воріт. В решті решт, разом з нашими партнерами, компанією Онеро привезли та провели монтажні роботи. Втім не лише вони брали участь в проєкті.
2. Специфічні умови вентиляції. Для цього використовують великі важкі вентилятори з різними режимами. Для кожного з них потрібно було передбачити окреме місце на складі. Наче нічого складного, окрім одного але...
Склад холодний, вага вентилятора не дозволяла кріпити їх просто на стіну.
Але оскільки склад холодний, вага вентилятора не дозволяла кріпити їх просто на стіну. Тож під кожен потрібно було виготовити власний каркас з профілів від виробника. Це додало процесу додаткової модерації щодо узгодження розмірів рам під фактичні розміри вентиляторів. Дивіться, як це виглядає зараз.
3. Склад без розгалуженої мережі освітлення.
Площа потребувала як внутрішнього, так і зовнішнього освітлення, з датчиками ніч/день, численними роз’ємами та підключенням вентиляторів. Разом з нашим постійним партнером, компанією «Леткор», довелось добряче попрацювати над складними розрахунками щодо проєктування системи електрики. Але маємо результат. Успішний фінальний проєкт, що вже працює.
Звучить легко, виглядає красиво. Саме так на практиці виглядає те, до чого докладають руки професіонали. Вони зберігають наявні логістичні шляхи та покращують процеси. Роблять це в межах бюджетів та мають розгалужену мережу перевірених партнерів. Забезпечують постійність роботи завдяки тимчасовим мобільним рішенням.
Тож може припиніть чекати до поки ваша капітальна споруда буде введена в експлуатацію? Швидкомонтовані споруди працюють тут й зараз, а Склад Сервіс на зв’язку майже 24/7. Звертайтеся.
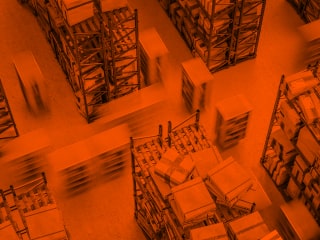