Зонуйте склад правильно! ТОП-10 правил
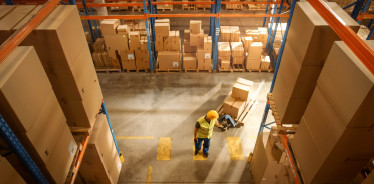
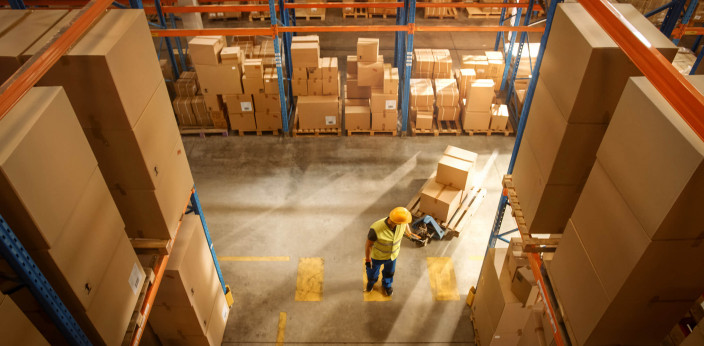
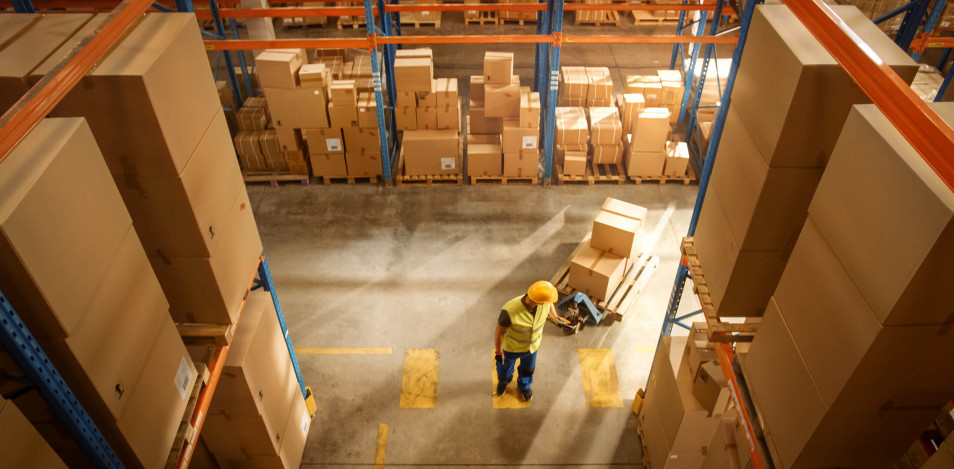
Якщо ваш бізнес пов'язаний з продажами - правильна організація системи складського зберігання товарів надасть перевагу перед конкурентами і підвищить якість обслуговування клієнтів. Одним з ключових кроків на цьому шляху є коректне визначення робочих зон складського приміщення.
Однак, на етапі розвитку бізнесу не всі володіють достатнім досвідом, щоб грамотно організувати складський простір. Зокрема, компактно розмістити вантаж, не порушуючи технологічні процеси і не створюючи дискомфорт персоналу.
Ми підібрали 10 рекомендацій, які підкажуть вам, на що потрібно звернути увагу при формуванні складу, а також зрозуміти, в чому причина «недоліків» складу, який вже функціонує.
Рекомендація №1. Не втрачайте швидкість в гонитві за щільністю зберігання
Перед вибором стелажів поміркуйте над тим, скільки часу витратить співробітник на вилучення та розміщення вантажів, особливо з верхніх ярусів. Пам'ятайте, що збільшення щільності ніяк не повинно позначатися на швидкості обробки вантажів. В іншому випадку підвищується ймовірність впливу людського фактора, де фахівці можуть витрачати більше часу і помилитися при розміщенні.
Рекомендація №2. Міжстелажне розташування та пропускна здатність - наше все
Мало хто знає, але збільшити щільність зберігання продукції можна не тільки шляхом спеціальних стелажів, але й завдяки скороченню операційних зон, міжстелажних проходів.
Бажано формувати ширину проходів, виходячи з розпорядку ваших виробничих операцій. Співробітники не будуть заважати одне одному та працюючій техніці, якщо ви складете чітку циклограму під кожен процес та візьмете до уваги ці дані під час розстановки обладнання.
Задачі з надмірною завантаженістю проходів іноді вирішують за допомогою WMS - системи, котра допомагає рівномірно розподілити вантаж площею приміщення. Для введення такої форми управління знадобиться цілий комплекс заходів: від аналізу товарних потоків до розробки схеми розташування продукції.
Рекомендація №3. Розподіляйте зону зберігання за принципом зниження трудовитрат
Сегментація зон зберігання - задача непроста, але досить цікава та навіть творча. Для встановлення оптимального порядку обробки та зберігання вантажів необхідно реалізувати моделювання, встановити властивості SKU та порахувати витрати на супутні процеси.
Власники нерідко вдаються до простого АВС - аналізу з динаміки звернень, під час котрого товари групи “А” розташовують ближче до зони відвантаження чи локації, де формуються готові замовлення.
А тепер уявіть ситуацію, що співробітникові необхідно обробити декілька товарів з різними фізичними характеристиками (важкий, легкий, крихкий). В якості прикладу візьмемо склад спиртних напоїв та простих закусок. Під час роботи з такими товарами необхідно не тільки дотримуватися точної послідовності для різного пакування (скло, поліетилен, жесть та т.ін), але й брати до уваги інші моменти. Так, більш крихкі пляшки слід комплектувати на важкі пластикові, а не навпаки.
У такому випадку, АВС-аналіз з динаміки звернень буде неефективним. Що дасть такий підхід, якщо крихкий товар розміщений ближче до зони вивезення, хоча його необхідно комплектувати в останній момент?
Якщо товар все ж розташований у вірній послідовності, то наступним кроком буде розміщення прибуваючих вантажів в комірках для зниження фізичних затрат працівника під час операції поповнення. Це дозволить зменшувавати трудовитрати в межах наскрізного процесу, а не автоматизувати операції у збиток загальному ефекту.
Рекомендація №4. Сортуйте вантажі на полицях за типами техніки, що використовується
Особливу увагу варто звертати на так звані “транзитні” ділянки складу, якщо є такі. Суть в тому, що в одній технологічній зоні може реалізовуватися обробка товарів шляхом різноманітних типів техніки. Оператору обладнання буде легше знайти необхідний піддон чи короб, якщо сформувати зберігання вантажів таким чином, аби в одній зоні розташовувались товари для конкретної одиниці техніки.
Не має значення, чи передбачена у вас система WMS - потурбуйтеся про максимальну ергономіку виконання процесів! Навіть в периметрі однієї транзитної зони можна організувати два повноцінні майданчики таким чином, що за відсутності засобів автоматизації співробітники будуть чітко розуміти, в якій частині складу зосереджена область їхніх задач.
Корисною буде хороша розмітка, особливо в умовах великих виробництв з великою інтенсивністю процесів, застосування конвеєрів, зонуванням. Тут важливо знизити вірогідність допущення помилок до нуля. Розмітку необхідно зробити таким чином, аби оператори чітко розуміли, де знаходиться ділянка їхньої відповідальності; могли чітко ідентифікувати товар.
Рекомендація №5. Рахуйте кількість ваших SKU
Мабуть, це одна з найпростіших рекомендацій. Однак, частими є випадки, коли під час проектування складу інженери беруть до уваги те, що одна номенклатурна позиція - не один SKU.
Реалізуючи аудит, спеціалісти можуть постановити, що на складі виділено 100 номенклатурних позицій, при цьому для продукції передбачено 150 місць. До уваги береться остаточний термін придатності продукції та дальність постачання вантажів. Адже якщо зіставити ці два показники, може виявитися, що вказаної кількості недостатньо.
Рекомендація №6. Продумайте схему буферизації товаропотоків між зонами складу
Часто на одному складі можна побачити картину, коли на різних ділянках виробничі процеси виконуються з різною інтенсивністю. На одних - швидше, на інших - повільніше. Для грамотної організації зони відбору спеціалісти рекомендують формувати буферні ділянки.
Для прискорення процесу обробки вантажів - відмовтеся від встановлення певних п’ятачків перед зонами контролю. Розробіть внутрішній порядок роботи буферних зон, встановіть ємність буфера та за допомогою розмітки обмежте територію для дотримання технологічної дисципліни співробітників.
Рекомендація №7. Деталізуйте ділянки для формування додаткових сервісів
Відсутність додаткових підзон може негативно відобразитися на ефективності та якості процесів. Краще розділити зону контролю та перепакування на окремі ділянки, адже самі собою операції на цих етапах є складними та всі 40% витрачаються на підготовчі операції: пошук тари, фасування та т.ін.
Рекомендація №8. Попереджуйте додаткове зонування, скорочуючи кількість типорозмірів місць
Рекомендуємо періодично аналізувати товарообіг на предмет висоти піддонів, котрі прибувають та покидають склад. За мінімальної кількості розмірів досягається універсальність складу та підвищення коефіцієнта використання функціонального об’єму.
Рекомендація №9. Орієнтуйтесь за ситуацією та змінюйте призначення зон складу, якщо є підстави
Не бійтеся реструктуризувати складські зони, якщо почастішала інтенсивність фрагментованого відбору продукції, змінилася динаміка відвантажень та т.ін. Проведіть аналіз для встановлення артикулів. Поставте задачу технологу складу: знайти баланс між об’ємом операцій на поповнення та підсумковим запасом зони набору.
Рекомендація № 10. Розраховуючи площу зон складу, не покладайтеся на «магічні коефіцієнти»
Всесвітня мережа Інтернет не скупиться на матеріали, присвячені так званим “магічним коефіцієнтам”. Згідно цій системі, зона приймання товару повинна вміщувати в собі приблизно 10% загальної площі складу, 20% повинно бути відведено на ділянку збору замовлення та т.ін. Безумовно, взяти до уваги подібну схему можна. Однак, для кожного складського приміщення, де товаропотоки, площі, технології абсолютно різні, ці величини завжди індивідуальні.
Сподіваємося, що наші рекомендації допоможуть вам правильно зонувати складський простір і ви зможете оптимізувати рутинні процеси і отримаєте максимум ефективності при мінімумі витрат часу і праці.